
Sustainability
QBG’s corporate objectives are simple: zero accidents, zero incidents, minimal impact on the environment and complete client satisfaction.
As such, we are committed to providing a safe and healthy work environment across all of our operations and eliminating and minimizing our environmental impact. To deliver on this objective, we proactively promote the highest standards in health, safety, security, environment and quality preservation and protection.
We do this through a formal Integrated Management System (IMS) for HSSEQ.
This allows us to:
- Identify all hazards and risks to our people, our clients and the environment.
- Prevent illness or injury by placing the highest priority on health.
- Set and review HSSEQ objectives and targets for continuous improvement.
- Ensure a close working partnership with clients to achieve mutually beneficial goals.
- Comply with country laws and regulations, corporate standards and other requirements.
Sustainability is the management and coordination of environmental, social demands and concerns to ensure responsible, ethical, and ongoing success. Sustainability is an integral part of QBG’s strategic plans. We conduct our business through our commitment, planning, and safety initiatives which is key to our continued success.
HSSEQ
Robust policies
QBG requires all managers, supervisors, employees and contractors to fulfil their legal responsibilities while consulting with staff and management to ensure the mutual health, safety and welfare.
To support our commitment and objectives, we:
- Promote a culture and ownership of HSSEQ responsibility and awareness through leadership, two-way communications and training.
- Apply the principles of Reduce, Reuse and Recycle to help prevent pollution and wastage.
- Comply with International Organization for Standardization (ISO) IMS to achieve ISO 9001:2008; ISO14001:2004; and OHSAS 18001:2007.
- Promote improvement through best practice techniques including reviews, inspections and internal audits.
- Investigate and report all accidents, incidents, near-miss events and non-conformances, to identify root causes and implement preventive measures.
- Provide adequate financial and physical resources to support our HSSEQ commitments.
Quality
QBG aims at providing the highest standards of quality and continuous improvement by utilizing a complete Quality Management System that is focused on operational excellence in preparation, management, and execution of tenders, projects, and contracts. The QMS incorporates the following:
-
Quality Management “QM”.
- Consistently provide quality service that meets customer and applicable regulatory requirements.
- Addressing customer satisfaction through the effective application of the system, including processes for continual improvement and the prevention of non-conformity.
- Employee empowerment to improve the department’s performance.
- Change management that will maintain a high level of service and continual improvement of the technical skill and capability.
-
Quality Assurance “QA”. Providing adequate confidence that the quality requirement of our customer has been met.
- Reliability: Deliver what was promised to our customers and clients.
- Competence: Making sure the staff delivering the service are competent and well trained.
-
Quality Control “QC”. Techniques and activities used to satisfy quality requirement.
- Verification: Ensure that the quality control activities are in place and effective.
-
Prevention: Identify/detect errors and ensure there is a system is in place for prevention. The following approach is implemented to answer the 5W’s:
- What error was made?
- Where it was made?
- When it was made?
- Who made it?
- Why was it made?
To support and provide the maximum value for our clients, QBG Management will establish the following goals:
- Do it right the first time.
- Demonstrate leadership and provide adequate resources and training.
- Assess risks and prioritize tasks/resources accordingly.
- All QBG employees will be responsible for meeting QBG’s quality standards and will be accountable for their own actions.
- All quality incidents will be noted and fully investigated to ensure corrective actions are implemented and communicated.
- Full comprehensive reporting and audit process is developed to measure QBG’s performance against set goals and objectives.
- Building “quality capability” through structured programs to ensure continuous improvement.
- QBG will ensure that its sub-contractors apply the same quality standards.
Integrated Management System
QBG’s Integrated Management System (IMS) is the driver in managing HSSEQ aspects, hazards and business controls at Qurum Business Group, including administrative management of the quality of products.
The integrated methodology is patterned after the deming cycle of Plan, Do, Check and Act, a cycle leading to continual improvement. As per the cycle, the following pillars apply:
- Plan: establish the objectives and processes necessary to deliver results in accordance with customer requirements and the organisation's policies and programs for managing environmental aspects and hazards to occupational health and safety, identifying customer requirements and meeting their expectations.
- Do: implement the processes defined.
- Check: monitor and measure the processes and products against policies, objectives and requirements for the products and report the results.
- Act: take actions to continually improve process performance.
Qurum Business Group has established, documented, implemented and maintains an integrated management system and continually improves its effectiveness in accordance with the requirements of ISO 9001:2008, ISO 14001:2004 and OHSAS 18001:2007.
Our management firmly believes in customer satisfaction and continual improvement in all spheres of its activity through establishment & implementation of the Integrated Management System. As such, the management of the company is fully committed to providing all assistance in the development, implementation and maintenance of the Integrated Management System and for its continual improvement.
Governance
QBG is committed to complying with the law and conduct business with the highest ethical standards by maintaining systems that ensure the highest levels of responsibility, integrity, and compliance.
Internal Audit
Internal auditing is an independent, objective assurance and consulting activity designed to add value and improve QBG’s operations. It helps QBG accomplish its objectives by bringing a systematic, disciplined approach to evaluate and improve the effectiveness of QBG’s systems, risk management, control, and compliance processes.
The Department of Internal Audit is an integral part of QBG and functions within established policies. Through its Group Head of Compliance, the department reports to the VC & GMD, with an open access to the Board, and conducts its responsibilities in accordance with QBG’s policies and procedures, and the Standards for the Professional Practice Framework of Internal Auditing issued by the Institute of Internal Auditors.
The Department's internal auditors will uphold the principles of integrity, objectivity, confidentiality, and competency.
Risk Management
Risk assessment is a systematic process for identifying and evaluating events (i.e. possible risks and opportunities) that could affect the achievement of objectives, positively or negatively. Such events can be identified in the external environment (e.g., economic trends, regulatory, and competition) and within an organisation’s internal environment (e.g., people, process, and infrastructure). When these events intersect with an organisation’s objectives or can be predicted to do so, they become risks.
To be effective, risk assessment cannot be merely a checklist or a process that is disconnected from business decision making. Rather, it should be integrated into the business process in a way that provides timely and relevant risk information to management.
The steps in carrying out a Risk Assessment are:
- Identify the Risk
- Identify Existing Control Procedures
- Evaluate the Risk
- Decide & Implement New Control Measures
- Monitor & Review
- Inform, Communicate, and Train
Contact Us - Oman
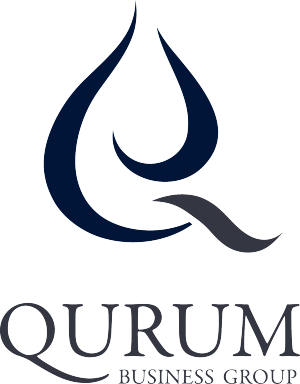
- Address: P.O. Box 614, Mina Al Fahal, P.C. 116, Sultanate of Oman
- Tel/Fax: +968 246 66000
- Fax: +968 246 66006
- Email: info@qurumbusinessgroup.com
Contact - United Arab Emirates
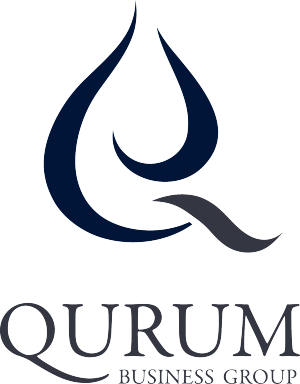
- Address: P.O. Box 15985, Dubai, United Arab Emirates
- Telephone: +971 4 551 2000
- Fax: +971 4 551 9381
- Email: info@qurumbusinessgroup.com
- Tenders: tenders@qurumbusinessgroup.com